Notting Hill Mews House Retrofit
Project Description
We delivered this retrofit for renowned Passivhaus architect Prewett-Bizley. Special features of this build include extensive use of Diathonite cork spray applied insulation. This product is both airtight and breathable making it the ideal solution to apply directly to existing brick walls of a period building with listed external features.
All sash windows are being replaced with new sash windows that feature vaccuum glazing. These will be shaded with external roller blinds concealed within six window dormers. Each intermediate floor conceals a minisplit AC unit. Heating and cooling is delivered by air source heat pump that feeds two separate highly insulated water tanks, one for cold water and one for hot.
The internals were extensively remodelled with a new staircase that opens up the interior of the building.
On the middle floor, glazed screens maintain a visual connection back to the staircase, making it an active part of the house. The landing here leads to a βsnugβ that doubles up as a spare bedroom. Despite the initial doubts of the client, this space is used every day as a home office, play area, and somewhere for the family to gather to watch TV. Elsewhere on this level is the primary bedroom and en suite, along with a series of cupboards housing cleverly concealed laundry facilities.
The top attic floor comprises childrenβs bedrooms, a bathroom and an en suite. A fully retractable roof light gives access to a roof-mounted air-source heat pump (ASHP).
The house is all-electric, with heating and, potentially, cooling provided by the ASHP. Its ventilation strategy is mixed-mode, with heat recovery in winter and natural ventilation in the summer.
In-use data after a year of occupation demonstrated an 82% reduction in energy consumption, meeting LETI requirements and exceeding the RIBAβs 2025 targets for new-build houses.
Had planning constraints permitted the installation of PVs, the architects think that operational energy use would have beaten the RIBAβs 2030 targets as well.
The projectβs carbon footprint has been assessed over its whole lifecycle, with both the embodied carbon of the retrofit and the operational carbon realistically appraised. The operational carbon is low enough to give a three-year payback on the embodied carbon.
The buildingβs clear and simple reconfiguration, along with its carefully specified and well-detailed fabric upgrade, delivers an exemplary family home with outstanding energy efficiency.
“Passing our air test the first time is testament to how well Bow Tie do things”
“My projects with Bow Tie are the only ones where Iβve left the contractor to follow my airtightness details and the projects have passed the 1st airtightness test.”
“We found Rafael polite and enthusiastic, and very quick to grasp what we wanted from the build – he has great communication skills.”
βWeβre expecting a dramatic reduction in costs. We now know how much energy weβve used (in March) and we rarely have the heating on compared to this time last year in our old house.β
βThe house definitely meets expectations and exceeds them in some areas, the heat comfort is very big, the noise is much less than it was, overall very happy with it.β
Interested in working with us?
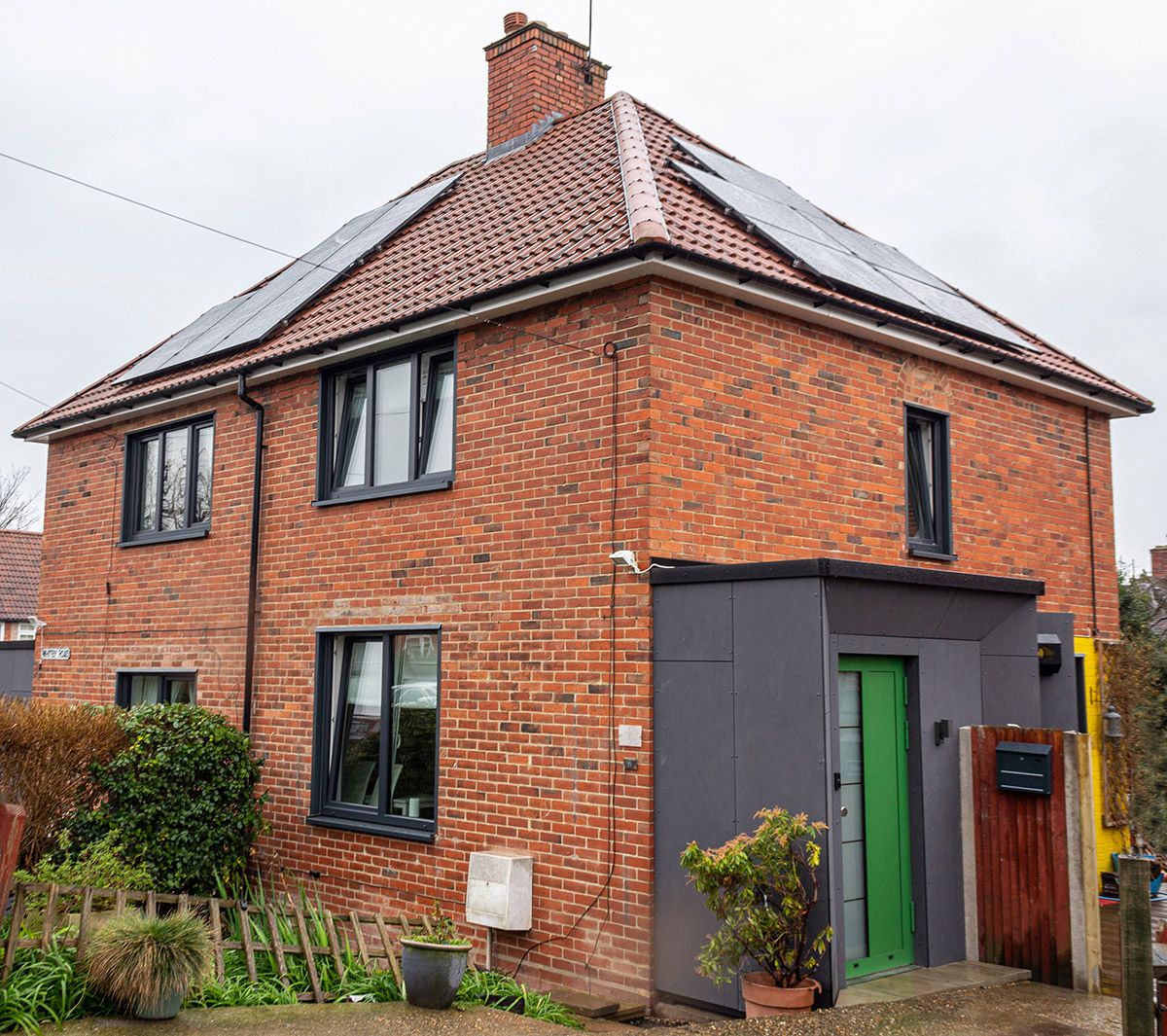
Sutton Energiesprong 6

Notting Hill Mews House Retrofit
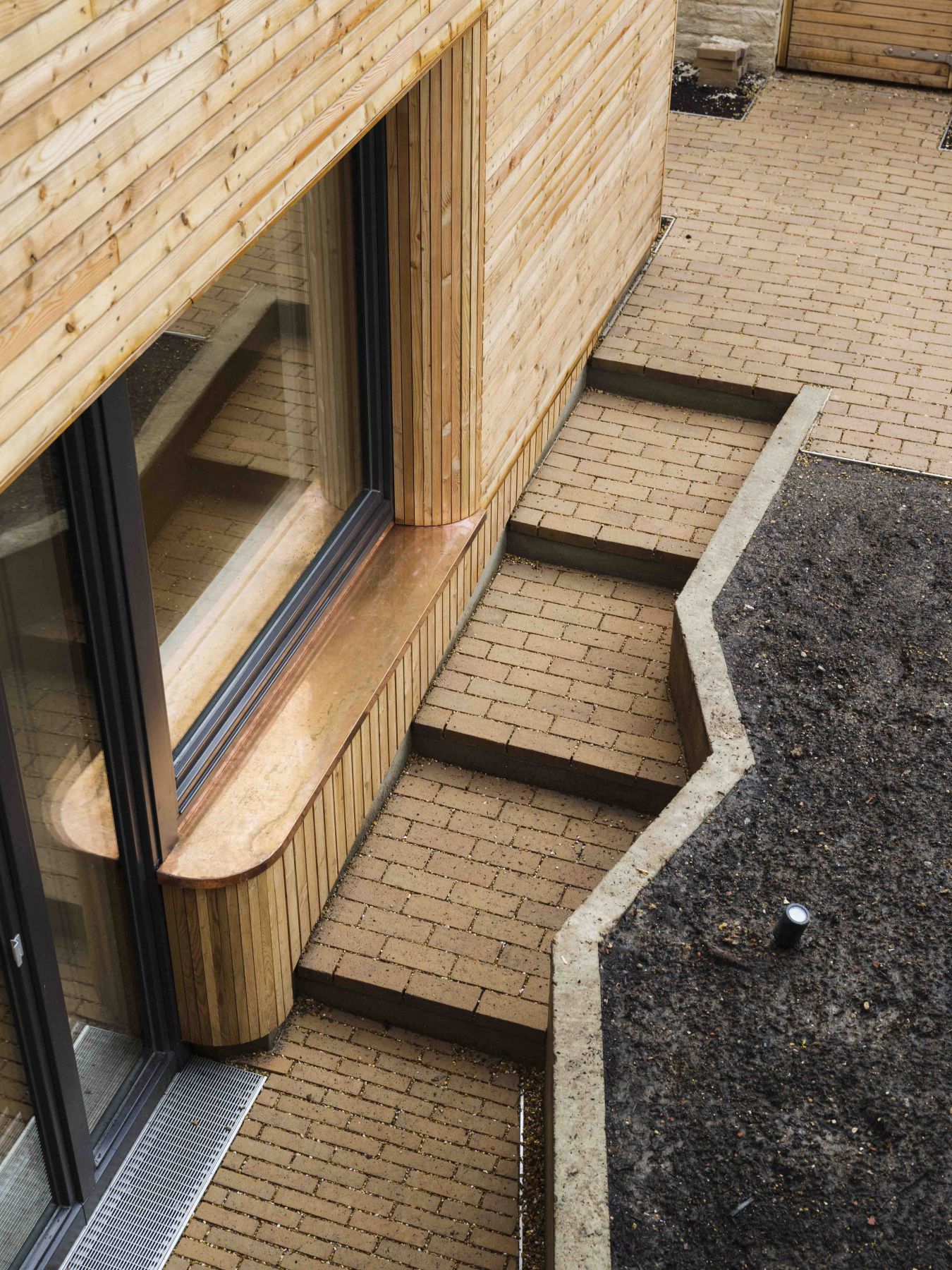
Max Fordham House
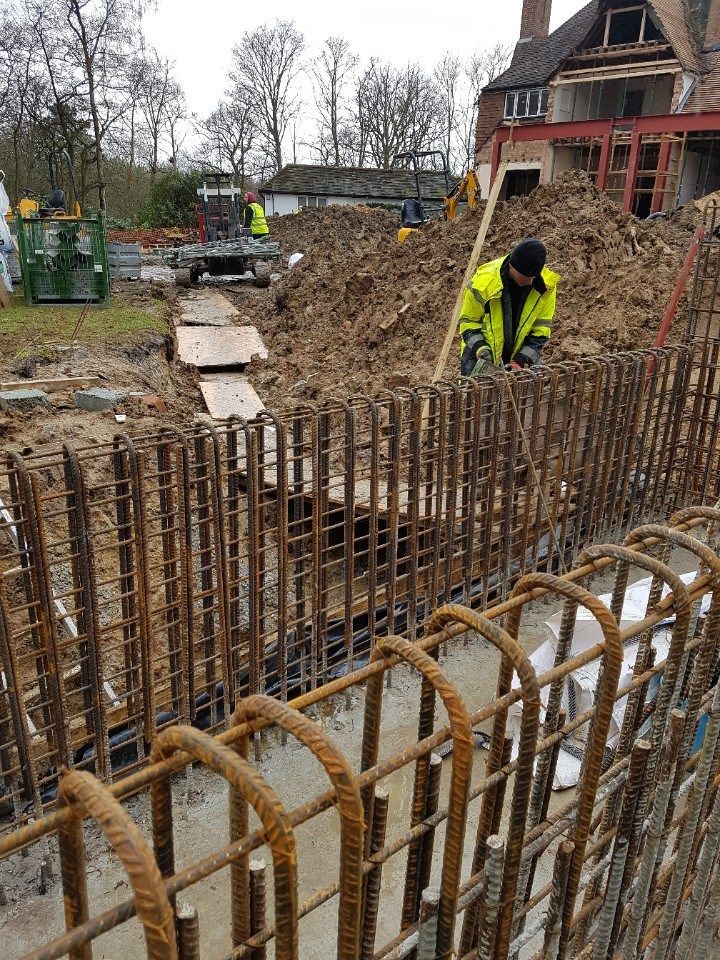
Potters Bar
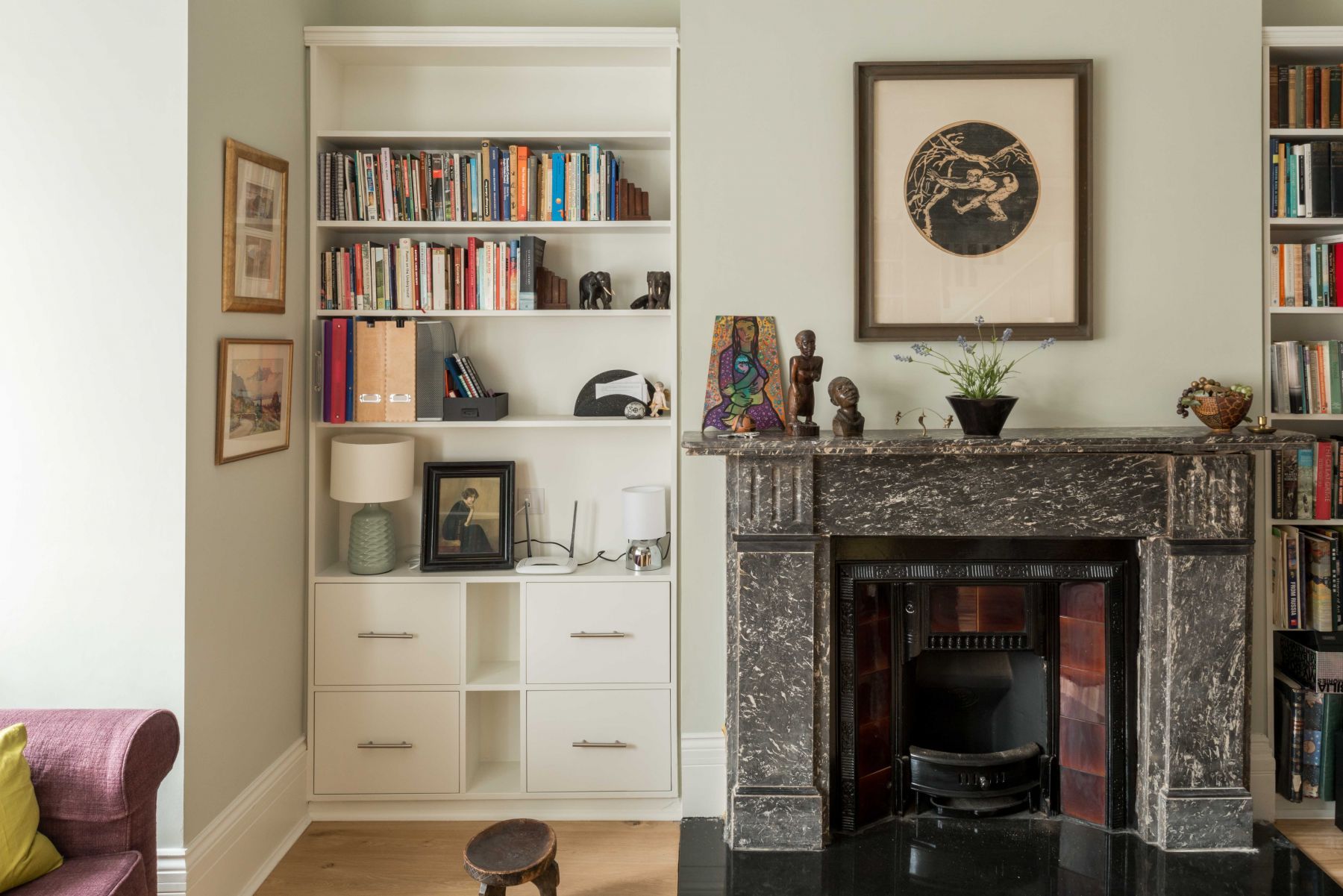
Muswell Hill EnerPHit
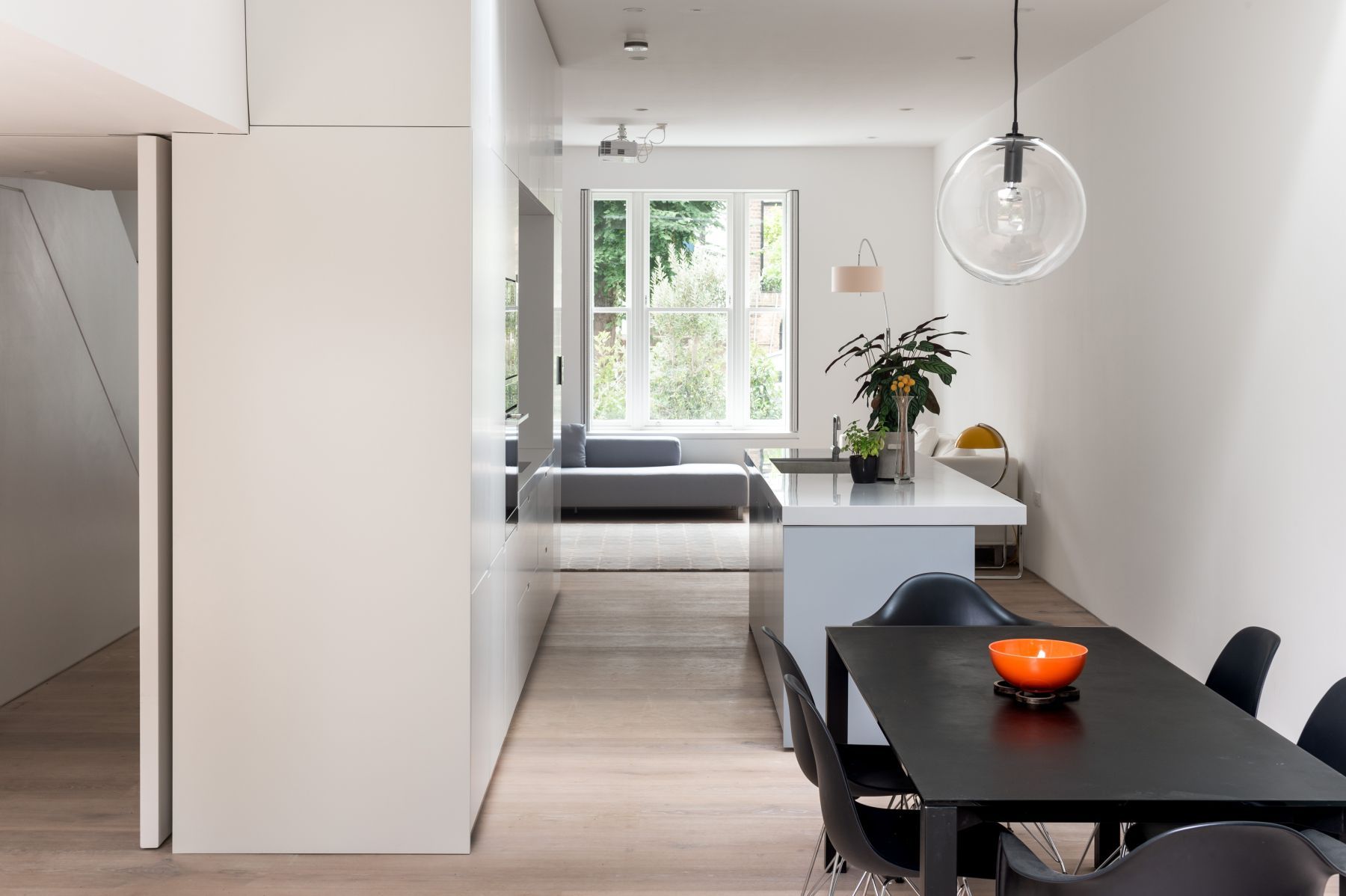
Kentish Town
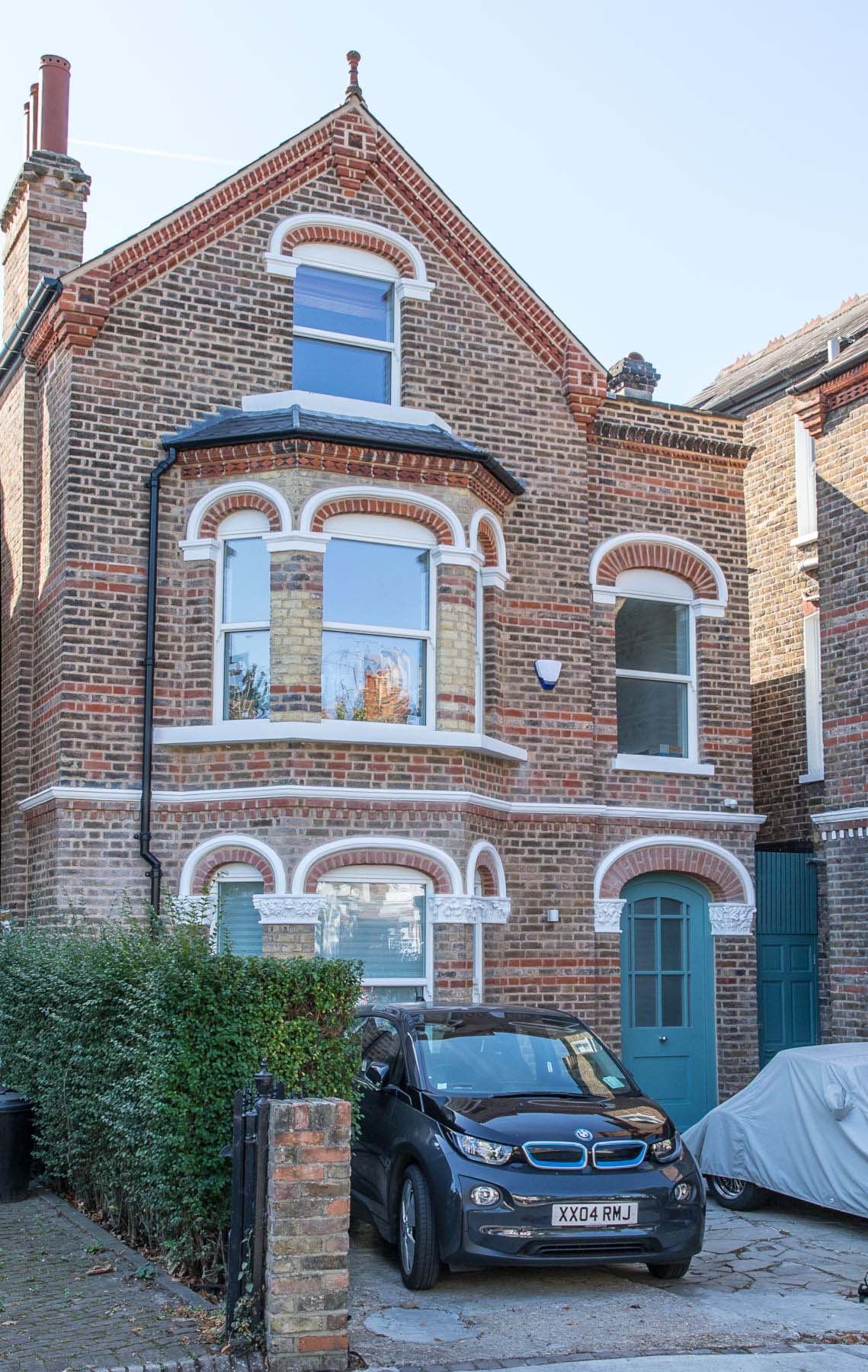
Stamford Brook
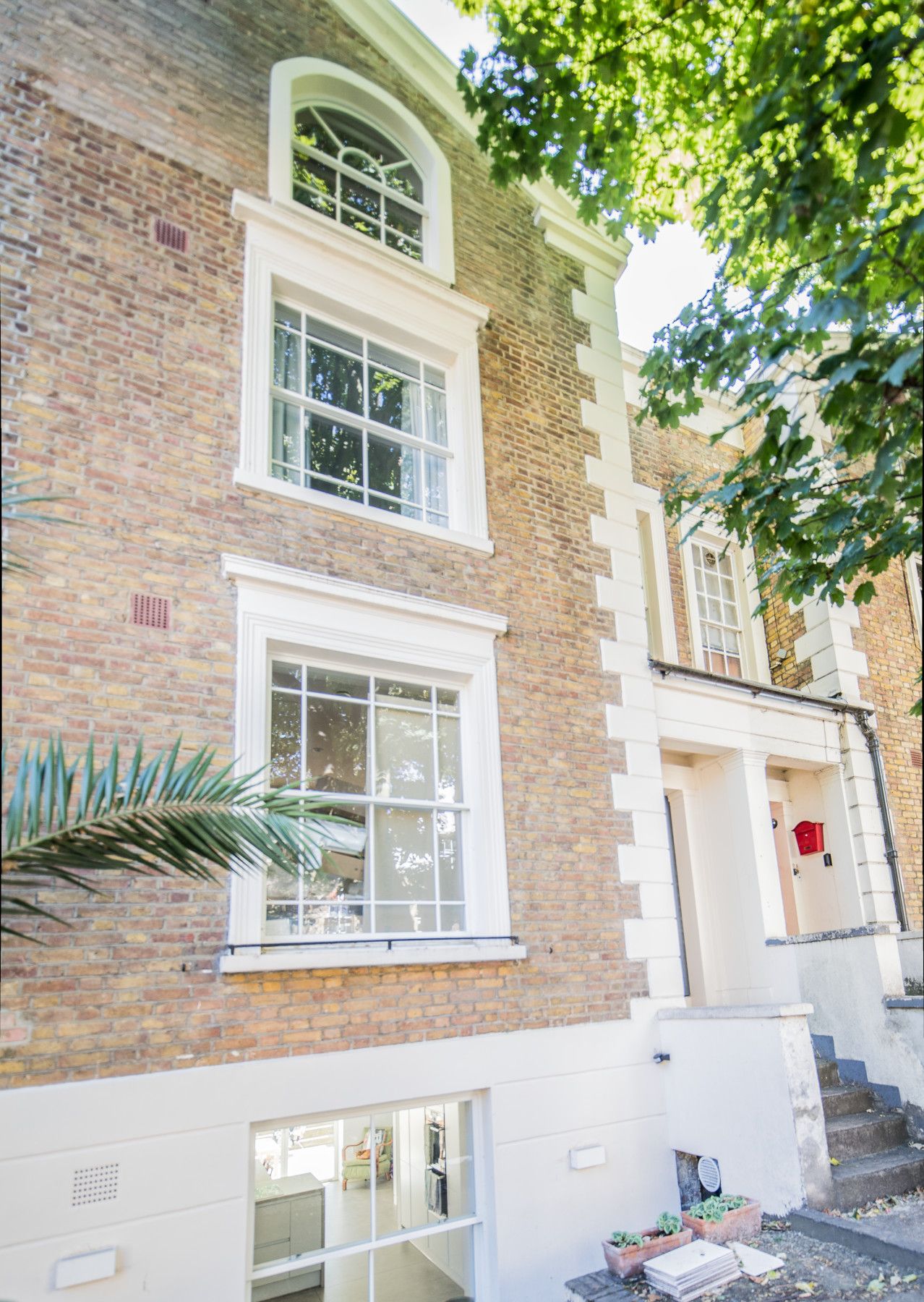
Kennington EnerPHit
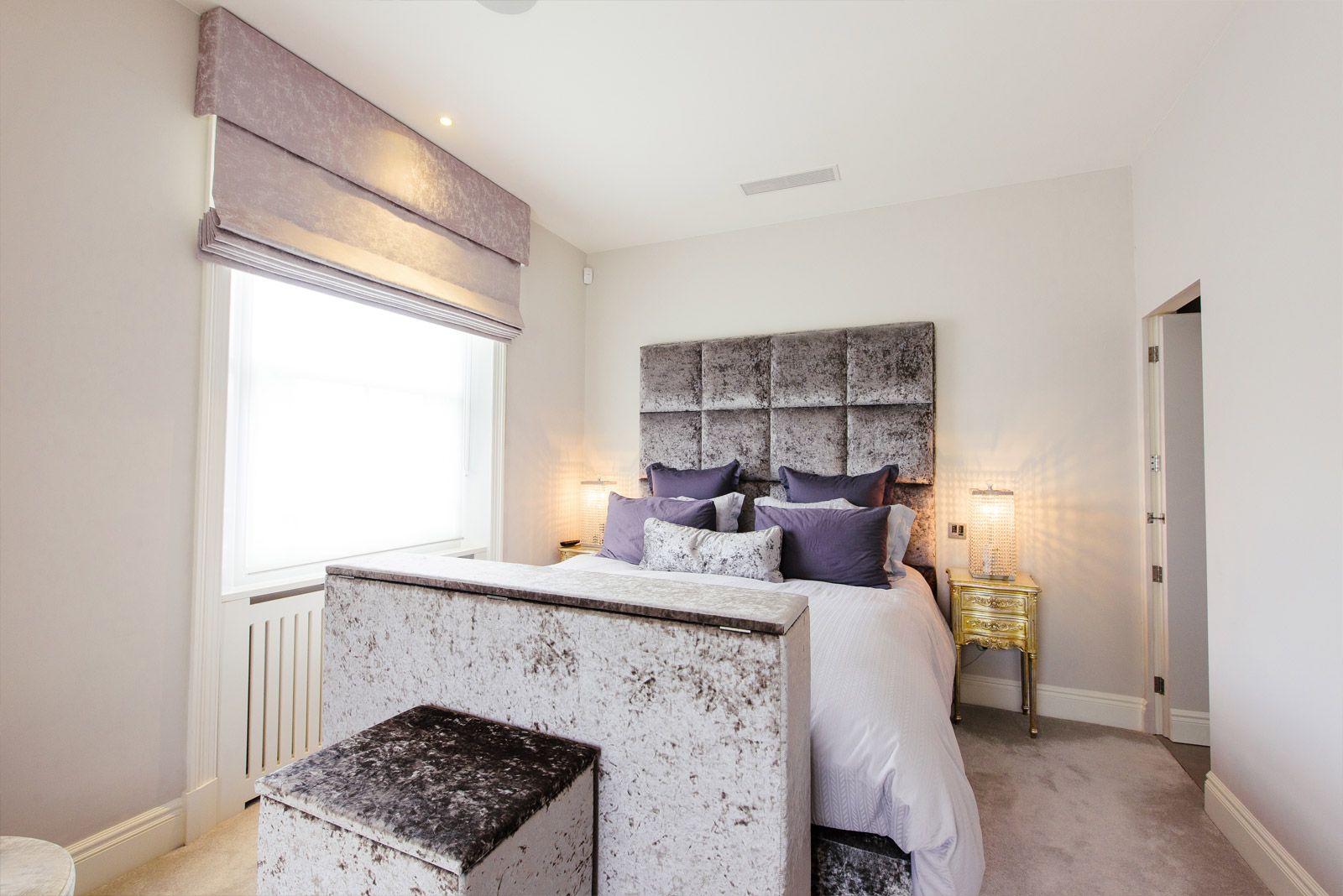
Maida Vale
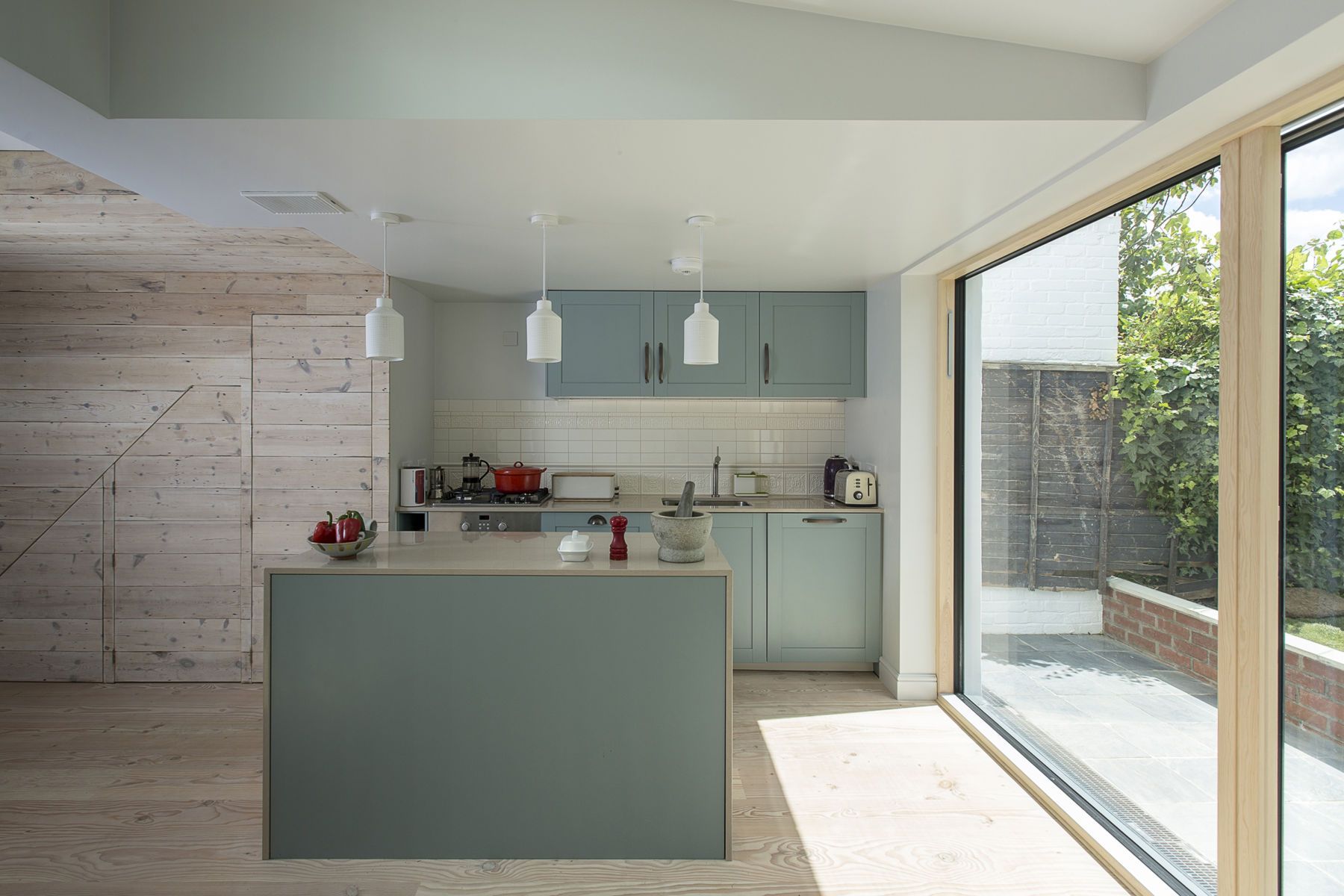
Tottenham

Angel
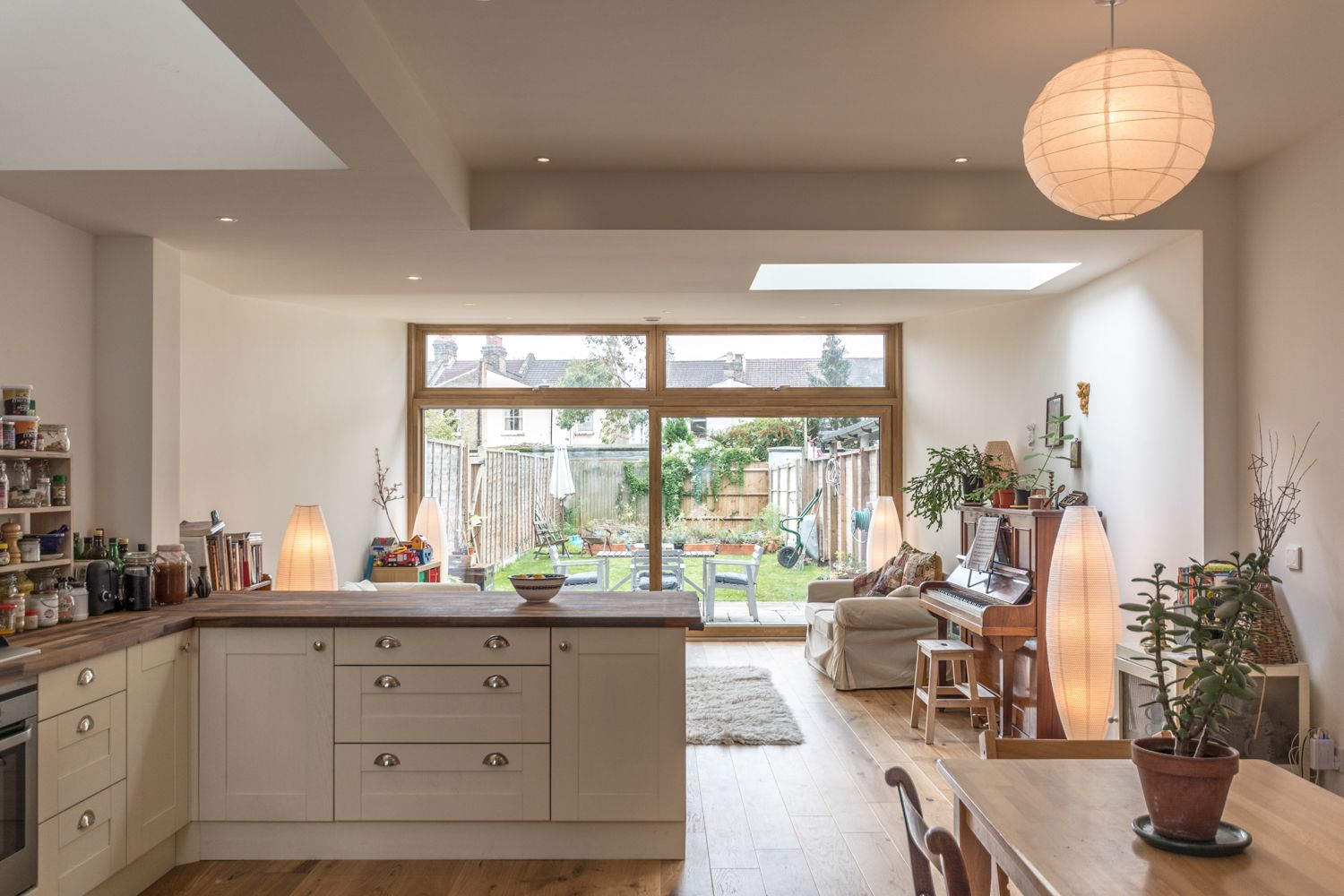
Bounds Green

Kensal Green Passive House
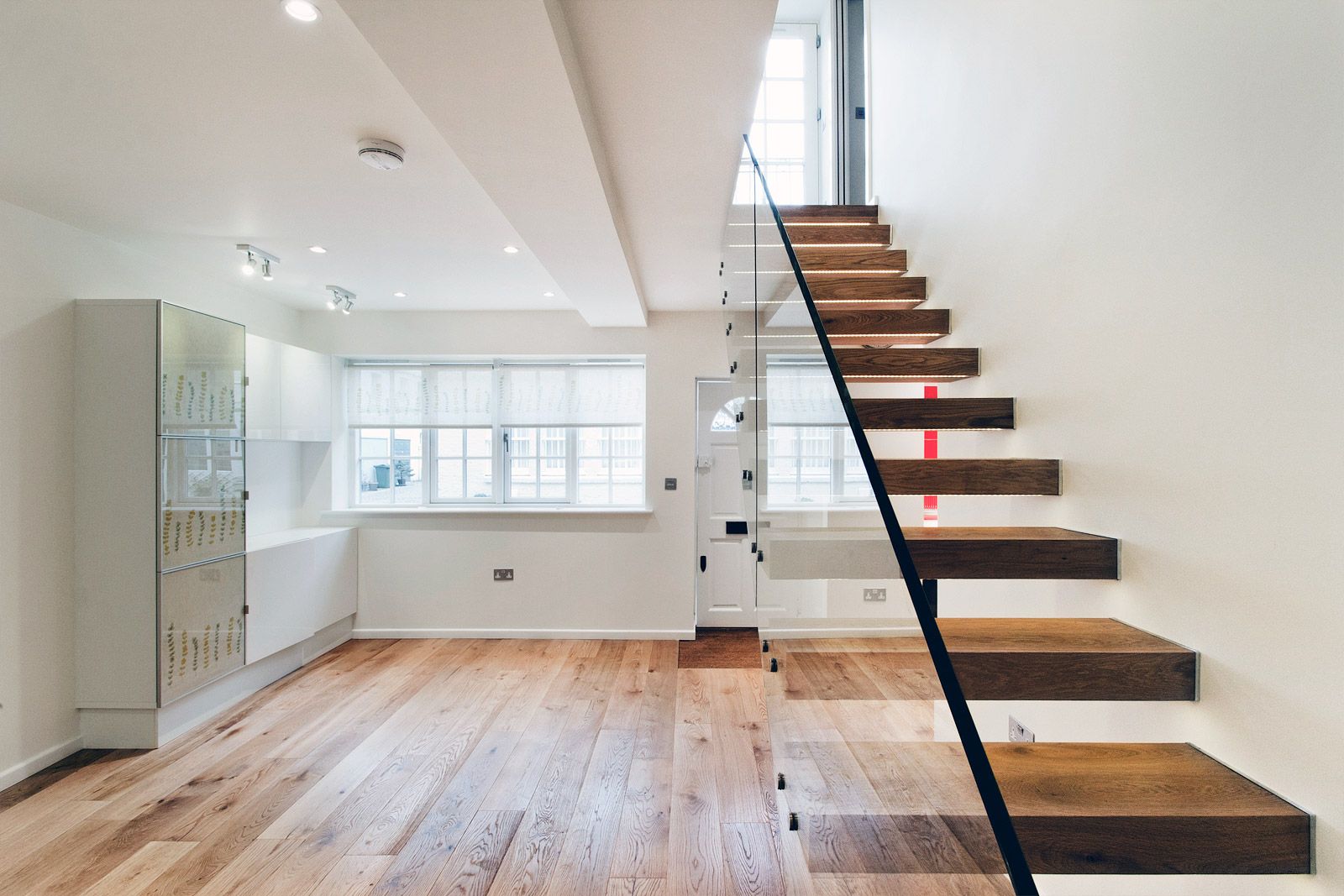
Bayswater
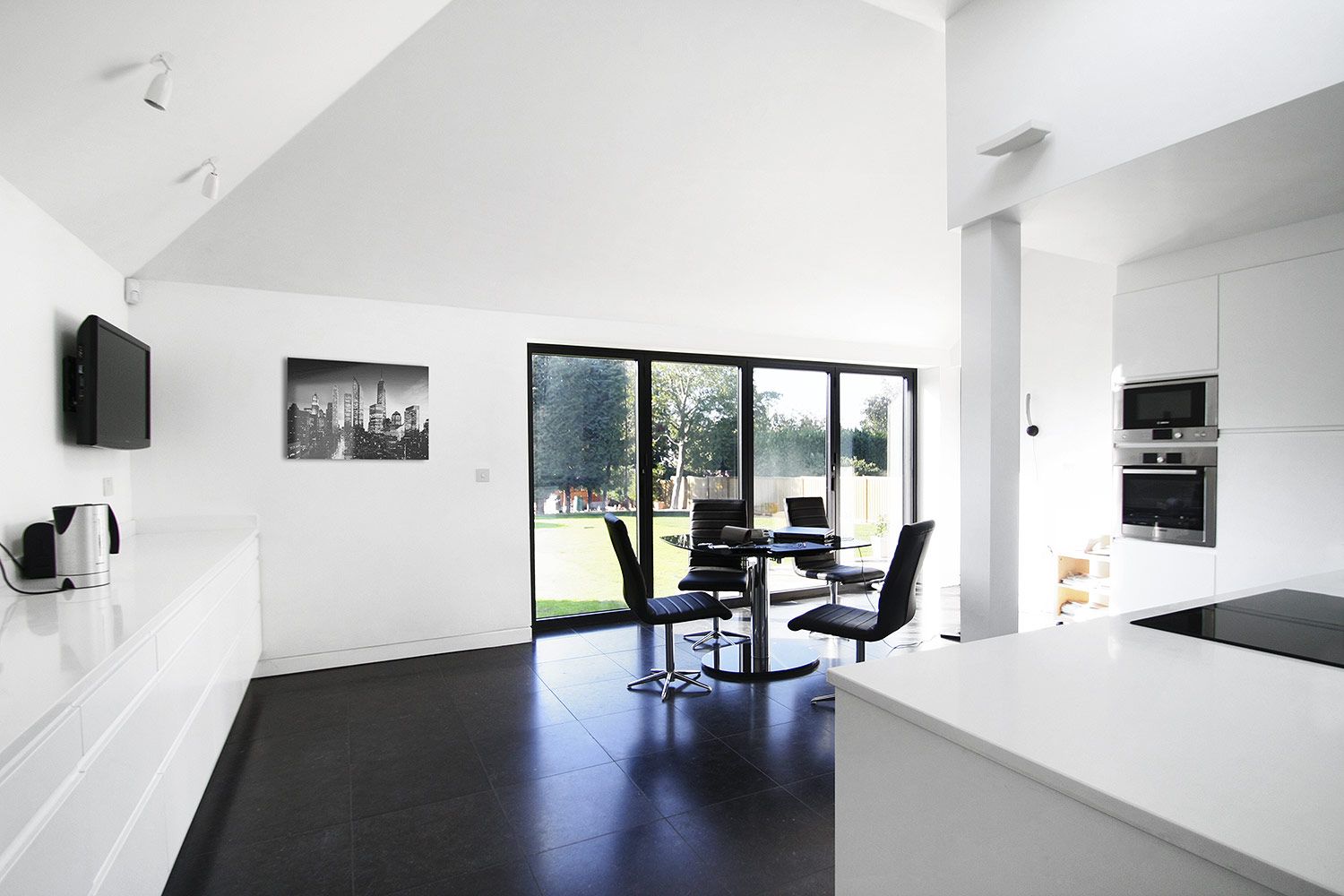
Arts and Crafts House
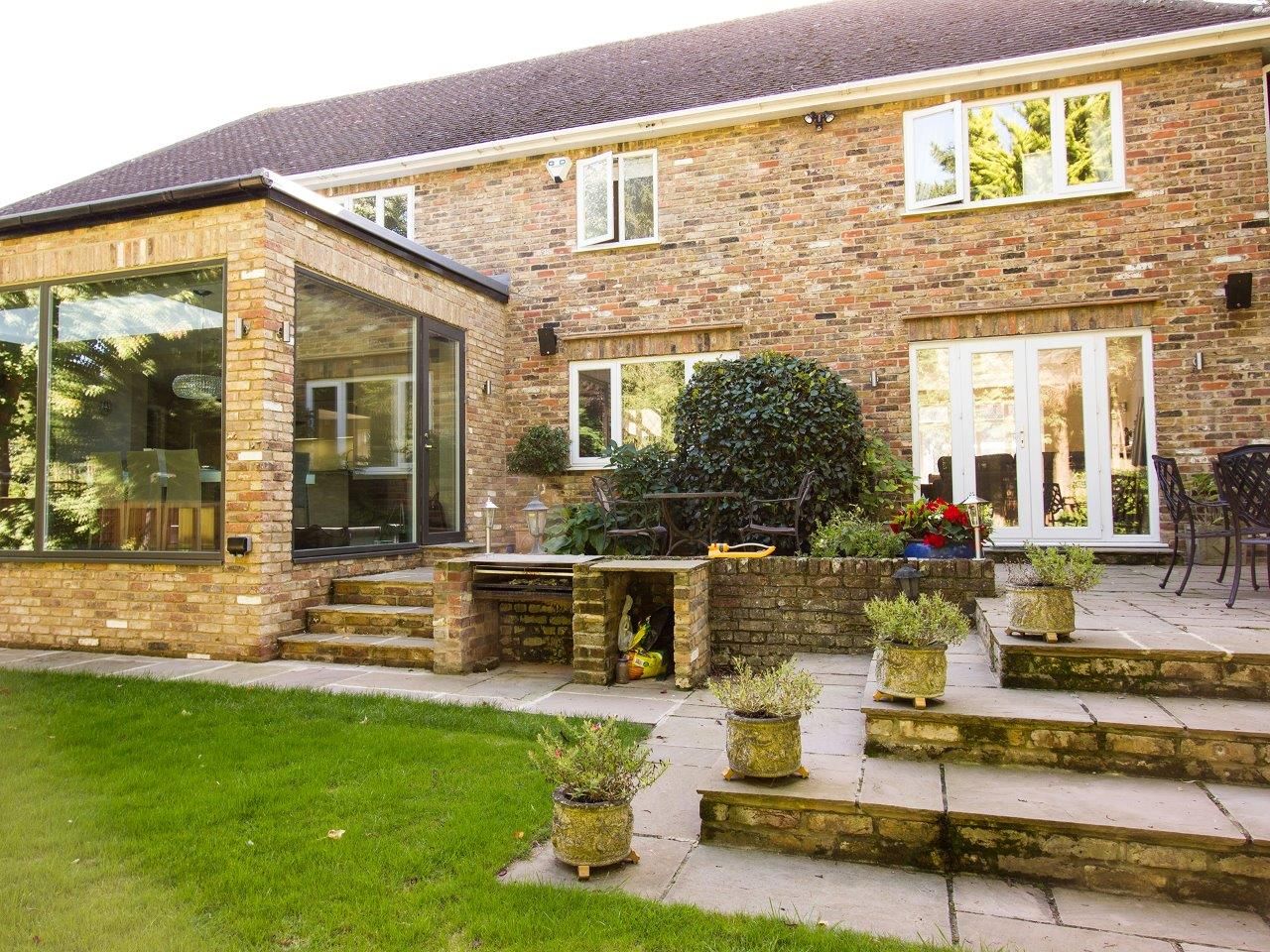